For traditional soap making with wood ash lye, you'll want concentrations between 10-20% by weight of oils, with 15-18% being ideal. Your lye solution should have a specific gravity of 1.2-1.3 and maintain a pH above 13. Test readiness using the fresh egg float method – when an egg floats one-third above the surface, you've hit the sweet spot. While these basic measurements work well, mastering the nuances of potash extraction will elevate your soap's quality.
Optimal Wood Ash Density for Potash Extraction
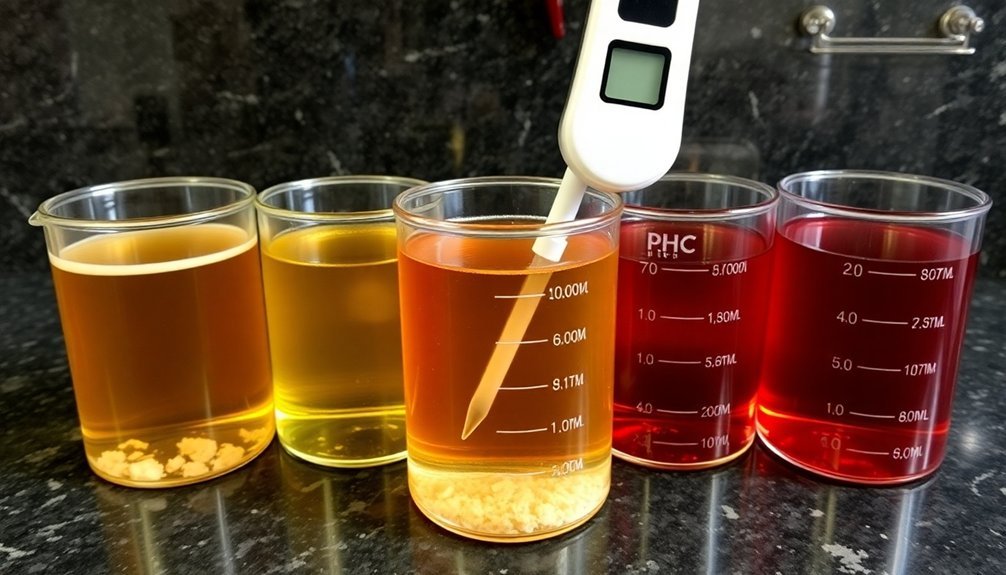
The science of potash extraction depends heavily on wood ash density, with hardwoods offering the best yields of 0.5% to 1.5% by weight. You'll find that hardwoods produce superior ash content, typically 6% to 10% by weight, making them your best choice for traditional soap making.
To achieve ideal wood ash density, you'll want to focus on maintaining higher purity levels during the burning wood process. Keep your temperatures lower to preserve potassium content, which averages 2.6% by weight in inland wood sources.
During the leaching process, avoid using dark or contaminated ash, as this can reduce your extraction efficiency. When you're careful about these factors, you'll maximize your potash yield and create better quality lye for your traditional soap making endeavors.
Base-Level Lye Measurements for Soft Soap
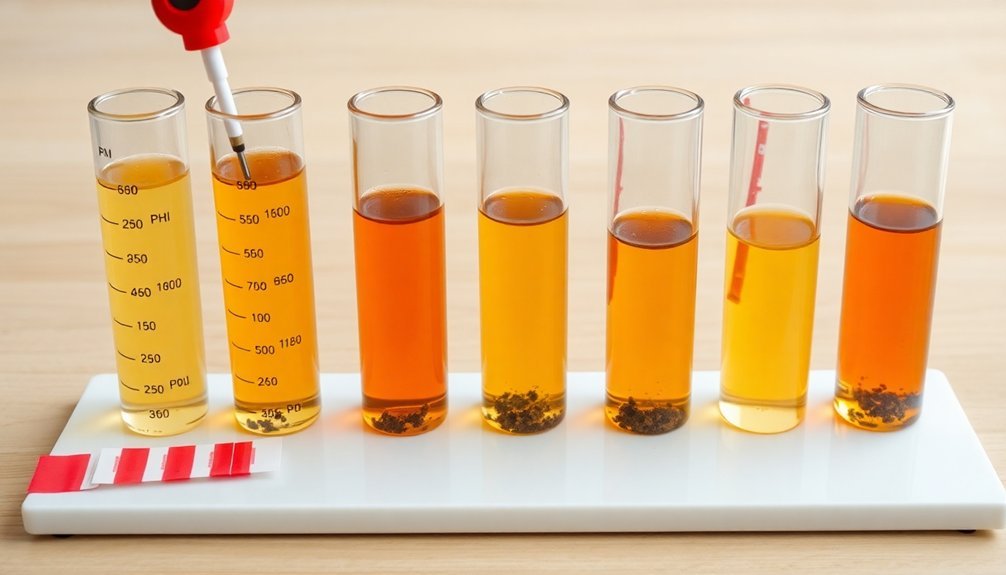
You'll need to achieve a minimum lye solution density of 1.18 for effective soft soap production, which you can verify using either a hydrometer or the fresh egg float test.
For ideal results, maintain a potash-to-water ratio that yields a specific gravity above 1.2, ensuring your solution has sufficient alkalinity for proper saponification.
When mixing your wood ash lye, carefully monitor these measurements since they directly impact your final soap's quality and consistency.
Measuring Lye Solution Density
When preparing wood ash lye for soap making, measuring the solution's density serves as a critical first step in achieving the right concentration.
You'll need to aim for a density of around 1.18, which you can measure using a hydrometer. To confirm you've reached the proper strength, try the egg calibration test – a fresh egg should float halfway above the surface of your lye solution.
If you're starting with a weak solution of about 1.2 density, you'll need to boil it down to concentrate it further.
Keep in mind that the ideal lye-to-oil ratio for successful saponification is 3:1, so precise measurements are essential.
You can also use alternative testing methods like floating a potato, as even small density changes can greatly impact your soap's quality.
Testing With Fresh Eggs
Testing lye concentration with fresh eggs offers a time-tested method for determining if your wood ash solution is ready for soap making.
You'll know you've achieved adequate strength when your egg floats with half its height above the lye solution.
For ideal soap production, you want your egg float test to show the egg maintaining about one-third submersion in the solution. If the egg sinks completely, your lye concentration isn't strong enough for saponification.
This traditional approach, while less precise than modern methods, provides a practical way to gauge if your wood ash lye will effectively create soft soap.
Remember that a properly floating egg indicates you've reached the right concentration to proceed with your soap making project.
While simple, this historical test remains a reliable indicator of lye strength.
Ideal Potash-Water Ratio Ranges
Three key ratios define the ideal potash-water balance for traditional soft soap making.
When using wood ash lye, you'll want to maintain a potash-water ratio between 1:3 and 1:5 for maximum saponification. The 1:3 ratio produces a more concentrated potash, ideal when you need stronger lye strength for specific recipes.
- Testing specific gravity should yield 1.2 to 1.3 in your solution
- Perform the egg float test – half-submerged eggs indicate proper concentration
- Hardwoods typically produce stronger lye than softwoods
- Adjust ratios based on your ash source and desired soap consistency
Standard Concentrations for Hard Bar Soap
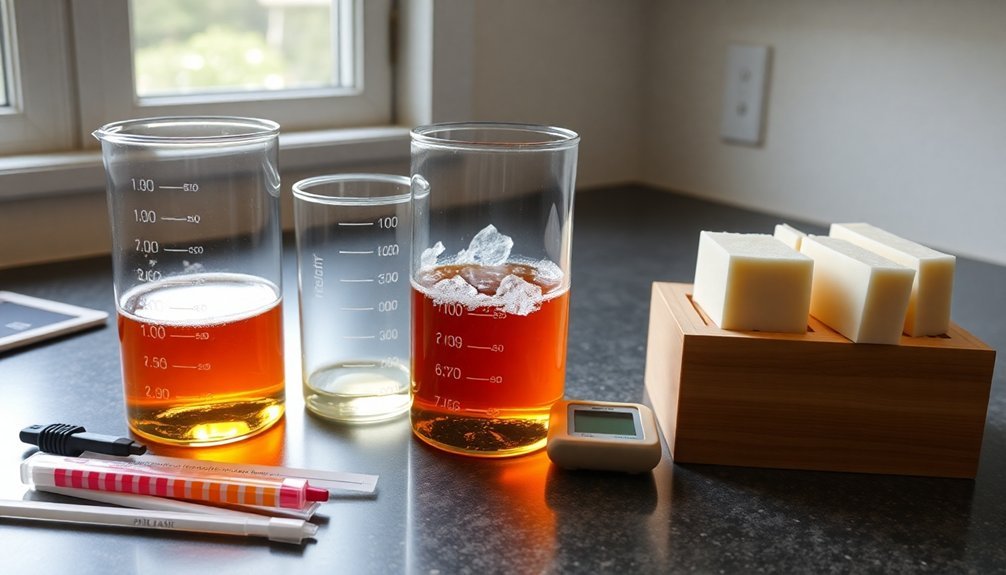
Although making hard bar soap with wood ash lye requires careful measurement, you'll need to maintain a 3:1 ratio of oils to lye solution for best results.
You'll get the best potassium carbonate concentration from hardwood ashes, which typically yield 0.5% to 1.5% ash by weight and contain about 2.6% potassium.
To achieve the ideal lye density for the soap making process, you'll want to test your lye concentration using the egg float method.
When your solution allows a fresh egg to float halfway, you've reached the right strength for saponification.
If your lye solution isn't strong enough, try boiling it down to reduce water content.
This concentration step is essential for creating firm bars that won't become too soft during use.
Testing and Adjusting Lye Strength
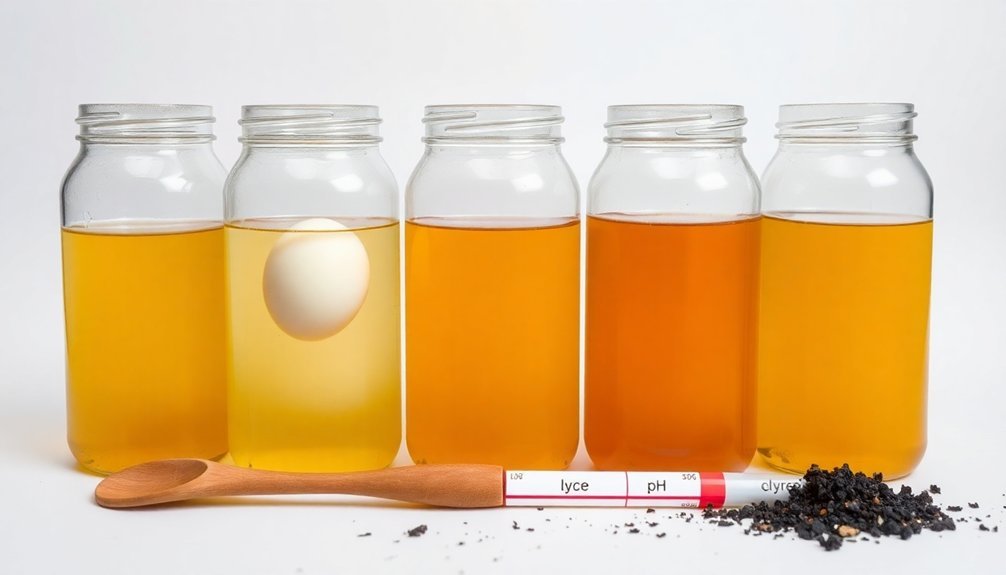
Proper lye strength sits at the heart of successful soap making. You'll need to test and adjust your lye solution to achieve the ideal concentration for saponification.
Using a hygrometer, aim for a density between 1.2 and 1.3, or try the egg float test where your egg should float halfway in the solution.
If you need to adjust your lye strength, you can boil the solution to reduce its volume and increase concentration. Monitor the density until it reaches approximately 1.18, and remember to maintain a 3:1 lye-to-oil ratio in your final soap making process.
- Use a hygrometer for precise density measurements
- Watch for the egg floating at halfway point
- Monitor solution while boiling to avoid over-concentration
- Test small batches first to perfect your measurements
Historical Potash Ratios From Colonial Records
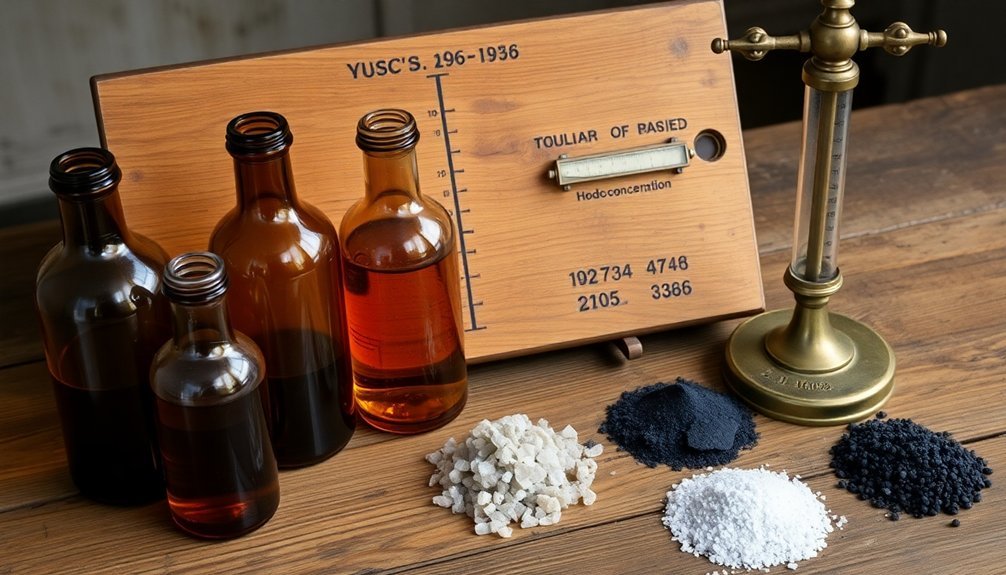
Colonial soap makers found that wood ash lye containing 2-5% potassium carbonate worked best for their soap-making needs, as shown in their detailed records and manuals.
You'll find that early Americans tested their lye concentration using a floating egg method, where proper strength was indicated when the egg remained suspended halfway in the solution.
The preferred use of hardwoods yielded 0.5-1.5% ash by weight, which you could then boil down to achieve the ideal 1:3 lye-to-fat ratio for effective saponification.
Colonial Soap Making Records
Historical records from early American settlements reveal fascinating insights into wood ash lye concentrations used for soap making.
You'll find that colonial soap makers achieved potash concentrations between 5% and 10% in their final products, depending on their wood source and process. They discovered that hardwoods like oak and hickory produced stronger lye solutions compared to softwoods.
- Colonial soap makers tested lye strength through trial and error
- They boiled solutions to increase potash concentration
- Wood ash sources greatly impacted soap quality
- Different leaching methods yielded varying lye strengths
Colonial records show that success in soap making depended heavily on both the wood ash source and extraction method.
You'd need precise ratios of ash to water to create effective lye solutions, a skill that colonial craftsmen developed through experience and careful documentation.
Potash Concentration Test Methods
Testing potash concentration emerged as a refined science during America's colonial period, building upon the trial-and-error methods of early settlers.
You'll find that colonial soap makers developed several reliable methods to test lye strength before beginning the saponification process.
The most common tests included using a hygrometer to measure solution density, where you'd want readings between 1.18 and 1.2 for ideal soap making.
Another proven method was the egg float test – if a fresh egg floated half-above the lye solution's surface, you'd achieved the right concentration.
Wood ash typically yielded 2.6% potassium by weight, and you'd often need to boil down the solution to increase potency.
For consistent results, you should maintain a 3:1 ratio of fats to potash lye when crafting your soap.
Early American Leaching Techniques
While hardwoods like oak and hickory proved most valuable for potash production, early American settlers developed systematic leaching methods to extract these precious alkaline compounds.
You'll find their traditional soap making relied heavily on precise measurements, using a 1:3 lye-to-fat ratio for successful saponification. The leaching process extracted potassium carbonate from wood ash using rainwater or distilled water in simple but effective setups.
- Hardwoods yielded 0.5% to 1.5% ash by weight, considerably more than softwoods
- Wooden troughs or barrels facilitated slow, thorough washing of ashes
- Rainwater proved ideal for dissolving alkaline compounds
- Multiple leaching cycles guaranteed maximum potash extraction
The resulting potash was less concentrated than modern lye, requiring careful testing and adjustment to achieve consistent soap quality.
Traditional Safety Thresholds for Soap Making
Because traditional soap making involves highly caustic materials, adherence to established safety thresholds remains critical for both novice and experienced crafters. You'll need to maintain wood ash lye concentrations between 10-20% by weight of your oils to achieve consistent soap quality. Always wear rubber gloves and goggles, as the alkaline nature can cause skin burns. Keep vinegar nearby to neutralize any accidental contact.
Safety Level | Concentration | Testing Method |
---|---|---|
Ideal | 10-20% | Hydrometer |
Acceptable | 15-18% | Egg Float |
Critical | >20% | pH Strip |
To verify your lye concentration, use a hydrometer or try the egg float test – when the solution's correct, your egg should float with half its height above the surface. Remember, proper concentration through careful boiling guarantees your soap's success.
Peak Alkalinity Levels for Maximum Saponification
Since achieving proper saponification depends on precise alkalinity, you'll need to maintain wood ash lye concentrations between 1.12 and 1.24 specific gravity.
Your lye solution's ideal saponification occurs when potassium carbonate and sodium carbonate balance at roughly 1.2 density.
Keep the pH level above 13 for maximum effectiveness, but don't exceed this threshold to avoid harsh soap.
Key indicators for proper alkalinity levels include:
- A specific gravity reading within the 1.12-1.24 range
- A potassium content of approximately 2.6% by weight
- A pH level maintaining above 13 but not excessive
- Positive float tests using eggs or potatoes
To confirm your lye concentration is suitable for soap making, always measure density before combining with fats.
This careful monitoring helps achieve the perfect chemical reaction for quality soap production.
Frequently Asked Questions
What Is the Best Lye Concentration for Soap Making?
You'll want your lye concentration to reach a density between 1.15 and 1.2 for ideal soap making. Test it by floating an egg – it should be half-submerged when your solution's ready.
How Do You Make Old Fashioned Lye Soap?
You'll need to mix wood ash with water to make lye solution, then combine it with heated fat at a 40:60 ratio. Stir until thickened, pour into molds, and let it cure for 4-6 weeks.
Can You Use 99% Lye for Soap Making?
Yes, you can use 99% lye for soap making. It's actually the preferred form for modern soap crafting, but you'll need proper safety gear and precise measurements to handle this highly concentrated chemical safely.
How to Make Lye From Wood Ash for Soap?
You'll need to sift wood ash, mix it with distilled water until milkshake-like, let it settle, then carefully pour off the clear liquid. Boil this down to concentrate your lye for soapmaking.
In Summary
You'll find success making traditional lye soap by maintaining wood ash concentrations between 5-7% for soft soaps and 8-12% for hard bars. Test your potash solution regularly and adjust based on your desired firmness. Remember to stay within historical safety thresholds of 13-15% maximum alkalinity. With proper measurements and careful monitoring, you'll achieve ideal saponification every time you craft these heritage recipes.
Leave a Reply