For successful cold process soap, maintain your lye and oils between 120-130°F for proper saponification. Keep these components within 10 degrees of each other to prevent false trace and guarantee smooth emulsification. After pouring, insulate your molds with towels or a heating pad to enhance the gel phase, but monitor for overheating signs like wrinkly textures. These temperature controls will transform your soaping experience from unpredictable to consistently professional-quality.
3 Temperature Tips For Better Cold Process Soap
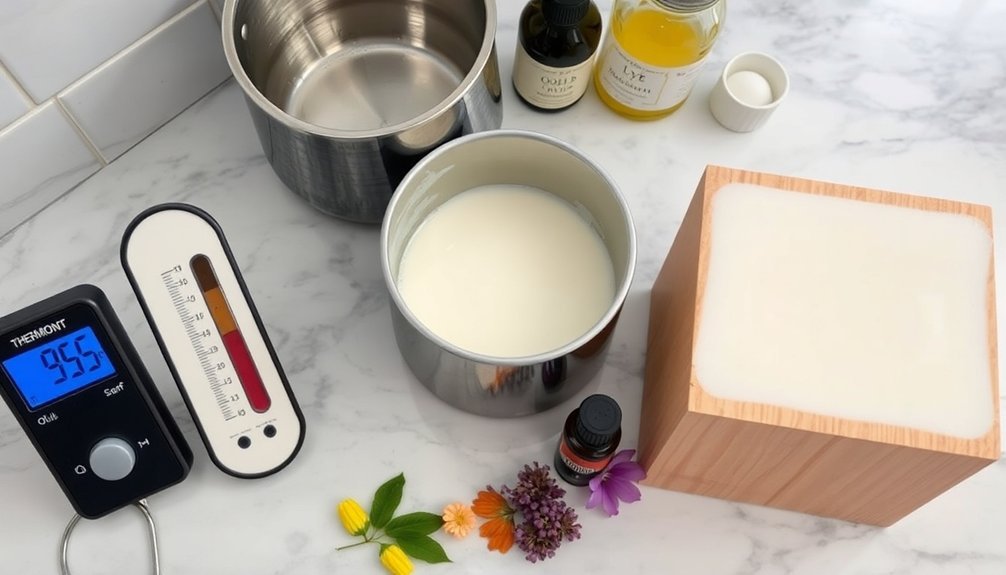
When it comes to successful cold process soap making, temperature control serves as your most powerful ally. Maintaining lye temperatures between 120-130°F guarantees proper saponification while preventing false trace, especially when working with hard oils.
Your soap mixture benefits from consistent heat monitoring throughout the process. After pouring into loaf molds, which naturally retain heat better than cavity molds, proper insulation methods become vital. Consider placing your mold in a box or applying a heating pad to enhance the gel phase, where temperatures may reach up to 180°F.
Check your soap after 30 minutes of insulation. If it feels cool or shows no signs of gelling, add a towel for additional heat.
But beware of overheating—wrinkly texture or soap rising from the mold indicates excessive temperatures that can compromise your final product's appearance.
Finding Your Ideal Temperature Range for Consistent Results
How consistently do your soap batches turn out? Temperature control is often the key to reliable cold process soap making. For most soap makers, the sweet spot lies between 120-130°F for both oils and lye solution. This range guarantees proper saponification while helping you avoid false trace issues.
Keep your oils and lye within 10 degrees of each other to promote a smooth chemical reaction. Hard oils and butters need sufficient heat to remain fully melted during mixing, but excessive temperatures can accelerate the process unpredictably.
If you prefer working in colder environments, try 100-110°F to prevent gel phase while still achieving complete saponification.
Remember that your lye solution starts extremely hot—up to 200°F—so always allow it to cool before combining with your oils for consistent results.
Mastering Heat Control to Prevent Common Soap Defects
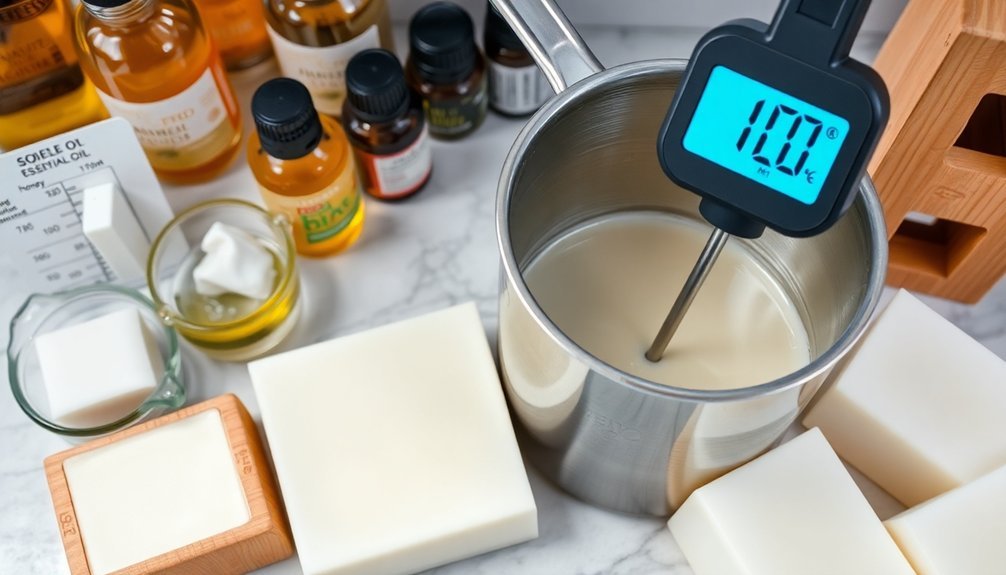
Temperature management stands at the heart of preventing common soap defects that plague even experienced crafters. Maintaining your soap making oils and lye water between 120-130°F guarantees your mixture becomes fully emulsified, helping prevent false trace during the process.
The gel phase represents a critical temperature milestone where proper insulation can enhance color vibrancy while preventing soda ash and glycerin rivers. If your soap feels cool after molding, add a towel or heating pad to encourage proper gelling.
Watch for signs of overheating like wrinkly surfaces or rising soap—immediately move your mold to the freezer if you spot these warnings.
For consistent results, try the heat transfer method, which uses the natural heat from lye water to melt oils while keeping everything within the ideal temperature range for cold process soap.
Frequently Asked Questions
What Is the Best Temperature to Make Cold Process Soap?
You'll get the best results making cold process soap at 120-130°F for both oils and lye. Keep them within 10°F of each other to guarantee proper saponification and prevent issues like false trace.
Why Add Salt to Cold Process Soap?
You'll add salt to your cold process soap to create harder, longer-lasting bars. It provides gentle exfoliation, reduces soda ash formation, and enhances lathering properties when used at 1-3% of your oil weight.
What Is the Optimum Temperature for Saponification?
You'll get the best saponification results by keeping both oils and lye between 120-130°F. Make certain they're within 10 degrees of each other to prevent false trace and guarantee smooth, successful cold process soap.
What Happens if Cold Process Soap Gets Too Hot?
If your cold process soap gets too hot, it'll enter gel phase, potentially causing alien brain formation, soap volcanoes, glycerin rivers, and wrinkly texture. You can cool it quickly in the freezer to minimize damage.
In Summary
Temperature management is your secret weapon for successful cold process soap. You'll avoid common pitfalls like separation, volcanic eruptions, and accelerated trace by finding your ideal temperature range and sticking with it. Remember, cooler temps give you more working time, while warmer batches speed things up. Trust your process—once you've mastered temperature control, you'll create beautiful, consistent soap batches every time.
Leave a Reply