Batch size greatly impacts soap unmolding due to heat retention dynamics. Larger batches trap more heat, promoting faster saponification and harder soap that's ready to unmold in 24-36 hours. Smaller batches cool quickly, often bypassing the gel phase, resulting in softer soap requiring 48-72 hours before unmolding. Your mold selection matters too—silicone works best for larger batches, while wider, shallower molds promote even cooling. Understanding these thermal principles will transform your unmolding success rate.
The Science of Heat Retention in Small vs. Large Soap Batches
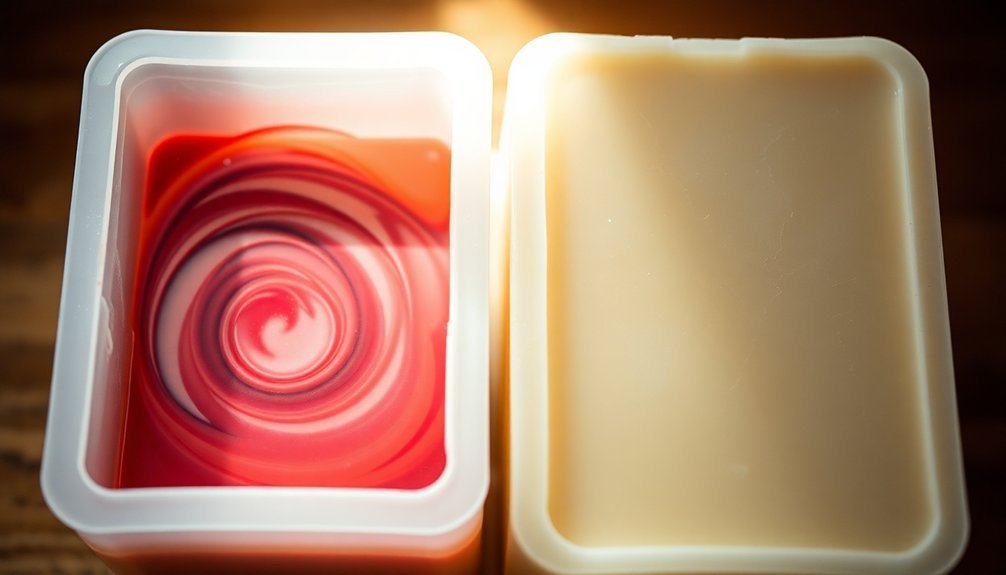
When crafting handmade soap, batch size greatly influences how your soap retains heat during saponification. Larger batches contain more lye and oils, creating greater thermal mass that traps heat effectively, promoting a successful gel phase. This internal heat pushes saponification forward, resulting in harder soap that's easier to unmold.
Your smaller batches cool much faster, potentially preventing complete gel phase. Without sufficient heat retention, the saponification process may slow down, leaving you with softer soap that's prone to denting or crumbling during unmolding.
Small batches often cool too rapidly, hindering gel phase and resulting in fragile soap that's difficult to unmold.
Temperature stability matters too—larger batches maintain consistent temperatures, reducing risks of separation and ricing that commonly plague smaller batches.
If you're struggling with unmolding issues, consider how your batch size affects heat dynamics throughout the soap-making process.
How Batch Size Affects Gel Phase Development
As your soap batch size increases, so does its ability to develop a full gel phase—that critical period when soap reaches peak temperature during saponification.
Larger batches naturally retain heat better, creating ideal conditions for this important shift.
When you work with smaller batches, you'll face challenges—they cool rapidly, often bypassing the gel phase entirely.
This can leave you with soap that's softer and potentially crumbly. The problem compounds if your recipe contains high water content, further inhibiting proper gel phase development.
For consistent results, consider that the gel phase typically occurs within 24 hours after pouring.
Larger batches benefit most from insulation methods, which maintain temperature and promote uniform soap texture.
This thermal advantage ultimately delivers a harder, more consistent final soap product that unmolds cleanly.
Optimal Timing: When to Unmold Based on Batch Volume
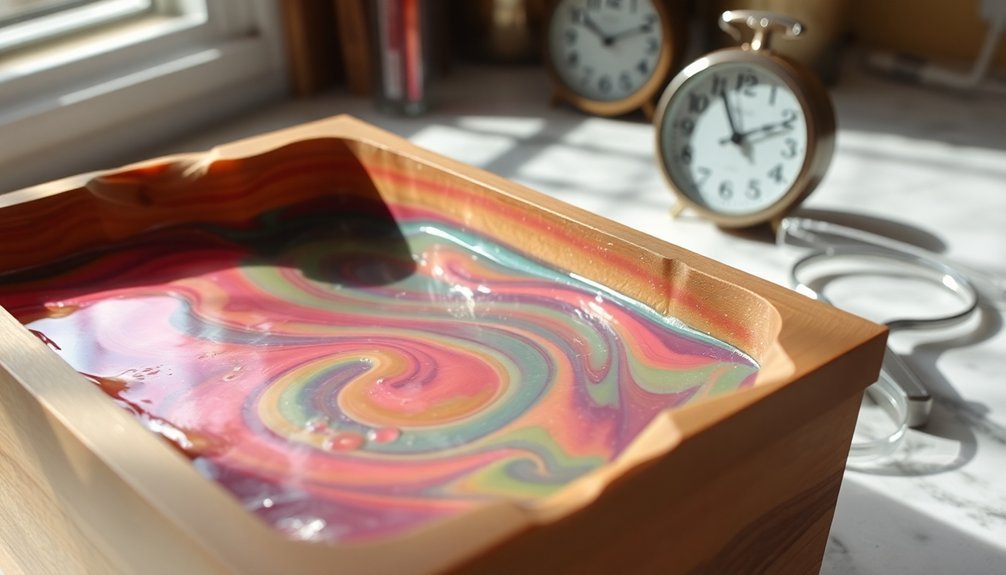
Your timing for unmolding soap largely depends on how your batch size retains heat, with larger batches typically requiring 36-48 hours before they're ready.
You'll need to adjust your schedule based on specific ingredients, as butter-heavy recipes may need extra time regardless of volume.
Watch for temperature cues—your soap should feel cool to the touch and firm enough to hold its shape before you attempt to free it from the mold.
Heat Retention Factors
The relationship between batch size and heat retention directly influences your soap's unmolding timeline. Larger batches maintain heat longer, often reaching gel phase—a critical stage that enhances hardness when unmolded.
You'll notice these batches typically require 24-48 hours before they're ready to unmold. Conversely, smaller batches cool more quickly, sometimes bypassing gel phase altogether, resulting in softer soap texture upon unmolding.
Environmental temperature variations further complicate this process; larger volumes need extended cooling time to prevent structural integrity issues like cracking.
Monitoring your soap's internal temperature provides valuable unmolding guidance—aim for approximately 120°F for ideal consistency. This guarantees sufficient saponification has occurred without compromising your soap's structure.
Ingredient-Specific Unmolding Schedules
Beyond temperature monitoring, specific ingredients in your soap formula greatly impact preferred unmolding times across different batch volumes. Your recipe's oil composition directly influences the soap's hardness and determines how quickly you can unmold.
Batch Size | Recommended Unmolding Time |
---|---|
Large (10+ lbs) | 24-36 hours (promotes gel phase) |
Medium (5-9 lbs) | 36-48 hours (variable gel phase) |
Small (2-4 lbs) | 48-72 hours (limited gel phase) |
Single Bars | 72+ hours (rarely reaches gel phase) |
High Hard Oil | 24-48 hours (regardless of size) |
Recipes with higher percentages of hard oils like coconut or palm will firm up faster during saponification, even in smaller batches. You'll need to extend curing times when using mainly soft oils. Consider wrapping larger batches to maintain ambient temperature and encourage the gel phase for ideal unmolding conditions.
Structural Integrity Challenges in Different Sized Batches
When you're working with larger batches, you'll notice they retain heat longer during saponification, which can lead to cracking or warping that weakens structural integrity during unmolding.
Smaller batches cool more quickly, resulting in more consistent textures and fewer unmolding challenges since they don't experience the same heat-related deformation risks.
The curing time variations between batch sizes greatly impact unmolding success—deeper molds used for larger volumes typically require extended curing periods to achieve the hardness needed for clean, damage-free removal.
Heat Retention Differences
Because soap-making relies heavily on thermal processes, batch size directly impacts your ability to unmold finished products with structural integrity intact.
When you work with smaller batches, you'll notice they cool faster, often preventing complete gel phase development. This results in soap that's more crumbly and challenging to unmold without damage.
In contrast, larger batches maintain heat retention more effectively, allowing thorough saponification and gel phase completion.
Your soap mixture's thickness in larger batches also contributes to prolonged warmth, resulting in smoother, firmer bars that release cleanly from molds.
Remember that ambient temperature affects this process too—smaller batches are particularly vulnerable to cool room conditions, which can compromise structural integrity.
You might need to extend the curing process for ideal unmolding results, especially in varying batch sizes.
Curing Time Variations
Heat retention is just one factor that affects your soap's unmolding success; curing time represents another critical variable that changes with batch size.
When you're working with larger batches, the increased heat generation often accelerates the gel phase, potentially shortening your unmolding timeline. However, don't rush—these larger batches may still require additional curing time to develop proper structural integrity throughout. The lye-to-oils ratio and water content must be carefully balanced as you scale up.
Conversely, smaller batches typically struggle to maintain sufficient heat, sometimes failing to reach gel phase entirely. This can leave you with softer soap that's trickier to unmold and requires extended curing time.
Environmental temperature and humidity further complicate these differences, affecting how quickly your soap hardens.
Always monitor your soap's hardness carefully—unmolding too soon leads to crumbly results, regardless of batch size.
Mold Selection Strategy Based on Batch Dimensions
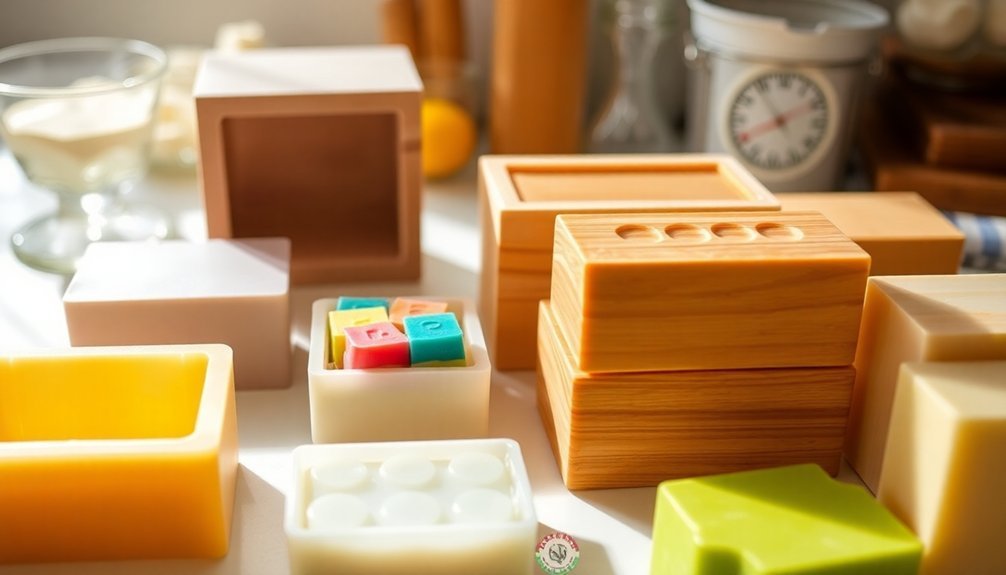
Since batch dimensions substantially impact the soap-making process, selecting appropriate molds requires careful consideration of your production volume.
For larger batches, choose silicone molds over plastic ones as they offer superior release properties and accommodate the extended cooling time needed for complete saponification.
When working with varying batch sizes, remember that deeper molds may cause uneven curing, particularly in the center where heat retention is greatest.
You'll find that wider, shallower molds promote more uniform cooling, resulting in consistent soap texture throughout.
To maximize predictability in unmolding, maintain standardized batch dimensions whenever possible.
This practice helps you develop reliable timing for when your soap has properly set.
Match your mold's dimensions to your typical batch size for best results—smaller batches in appropriately sized molds will cool more efficiently.
Adjusting Water and Lye Ratios for Varied Batch Quantities
When scaling your soap recipes up or down, you'll need to carefully adjust both water and lye ratios to maintain consistent quality across different batch sizes.
The standard 2:1 water ratio to sodium hydroxide works well for small batches, but large batches often benefit from water discounts to prevent excess moisture and facilitate easy unmolding.
As you increase production, accurate measurements become even more critical—minor errors can appreciably impact soap hardness and saponification.
Remember that larger batches generate more heat during the process, which affects the gel phase. You might need to adjust cooling methods accordingly to manage this increased thermal activity.
Consider implementing small water discounts (5-10%) for larger batches to improve unmolding success while maintaining proper chemical reactions.
Frequently Asked Questions
Why Is My Soap Not Gelling?
Your soap's not gelling because you're using low temperatures, insufficient water-to-lye ratio, or inadequate insulation. You'll need more heat, proper water content, and better insulation to encourage the gel phase properly.
What Are the Factors Affecting Soap Making?
Your soap making is affected by oil choice, lye concentration, temperature, additives, and technique. You'll also need to take into account cure time, fragrance levels, mold type, and environmental conditions like humidity and ambient temperature.
Why Is My Soap Curdling?
Your soap is curdling because your lye solution is too cool, you're using oils high in unsaturated fatty acids, you're mixing too vigorously, your measurements are off, or environmental factors like temperature and humidity are interfering.
Why Are My Soap Layers Not Sticking Together?
Your soap layers aren't sticking together because you're likely pouring at improper trace consistency or not allowing each layer to set properly first. Confirm similar temperatures between layers and mix additives evenly for better adhesion.
In Summary
When deciding on your soap batch size, you're actually controlling the unmolding experience. Larger batches retain more heat, speeding gel phase and often allowing earlier unmolding. You'll need to adjust your water-lye ratios accordingly and select appropriate molds that complement your batch volume. Remember, it's not just about quantity—it's about creating the perfect conditions for your soap to release cleanly and maintain its structural integrity.
Leave a Reply