To control batch heat while making soap, use stainless steel pots 25% larger than your batch volume, keep your oils and lye at similar temperatures (100-110°F), insulate coolers for consistent temperatures, use stick blenders in short bursts, select fragrances that won't accelerate trace, and test small batches first. Monitor temperatures with reliable thermometers and consider heat-treating oils beforehand. These techniques will help you achieve smooth, consistent results in your next creation.
7 Ways To Control Batch Heat While Making
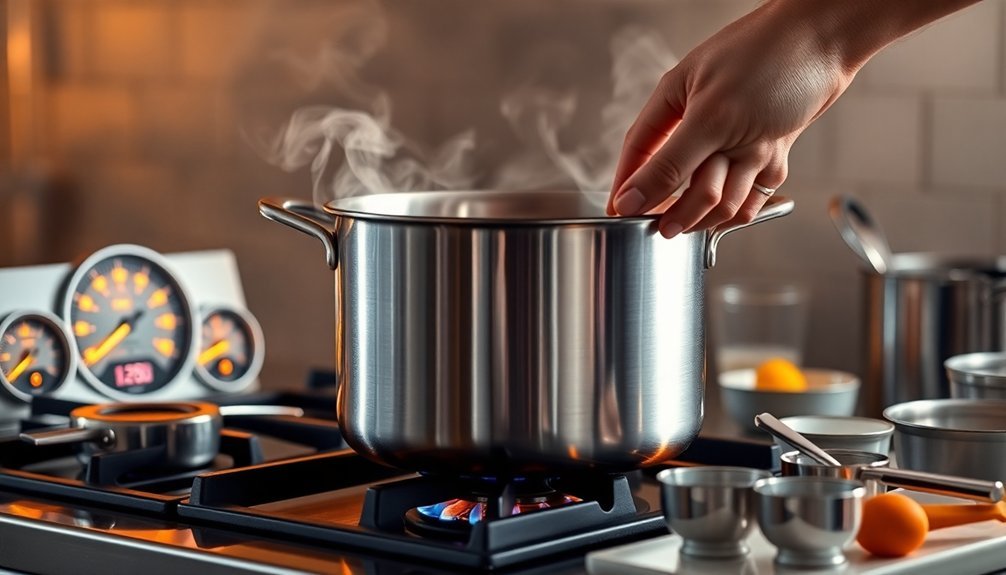
When brewing at home, maintaining consistent temperature throughout the mashing process greatly impacts your final product's quality. For small-batch brewing, you'll need effective temperature control strategies to minimize heat loss.
Preheat your oven to its lowest setting and place your mash pot inside, turning it off after initial heating. This creates a stable environment for your batch without overheating.
A pre-warmed oven creates the perfect temperature-stable sanctuary for your mash, preserving crucial enzymatic activity without excess heat.
Alternatively, use an insulated cooler as your mash tun by adding 170°F water and monitoring as you add milled malts.
Invest in reliable temperature monitoring tools like the Maverick ET-733, which provides precise readings for timely adjustments.
Don't forget to stir your mash regularly to prevent temperature inconsistencies throughout your batch.
Experiment with different methods—warm ovens, insulated containers, or trays for heat distribution—until you find what works best for your setup.
Selecting the Right Pot Size for Your Soap Formula
Just as brewing requires temperature control, soap making demands appropriate equipment selection for ideal results. Your pot size directly impacts temperature control and the success of the saponification process.
Choose stainless steel pots for their excellent heat distribution and durability during the chemical reactions of soap making.
- Select a pot at least 25% larger than your total ingredient volume—a 2-3 quart pot works well for standard 2-pound batches, preventing overflows while mixing.
- Consider pots with wider bases for better heat distribution, allowing you to manage temperature fluctuations more effectively.
- For batches exceeding 5 pounds, invest in larger vessels to maintain consistent heat throughout your mixture, ensuring even saponification.
The right pot size balances adequate space for mixing with proper heat management for perfect soap results.
Managing Temperature Differences Between Oils and Lye
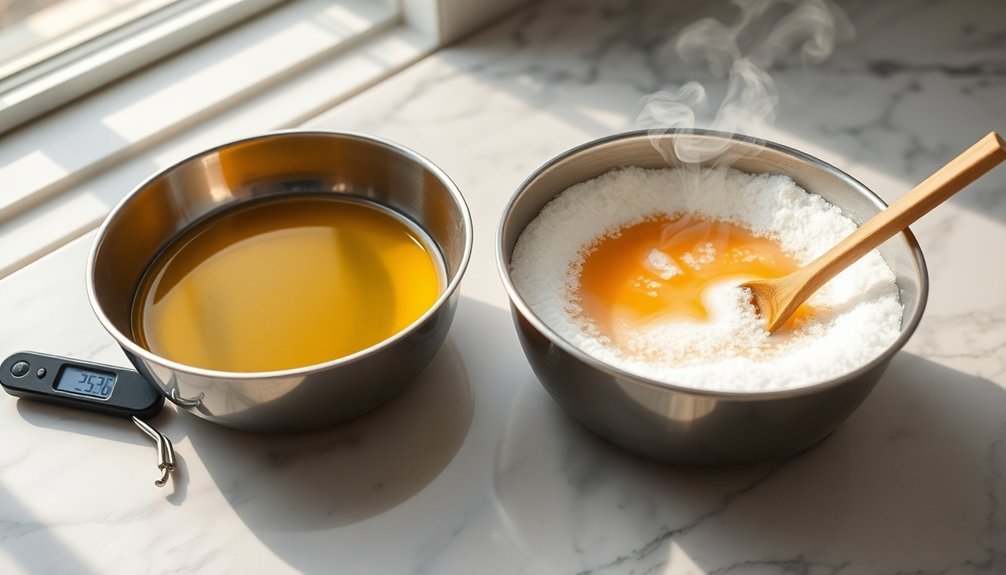
You'll need to synchronize your oil and lye temperatures (around 100-110°F) to prevent soap seizing during the mixing process.
Use a reliable thermometer to monitor both components, adjusting with gentle heating or cooling until they reach similar temperature points.
Consider insulating your mixing container to maintain stable temperatures throughout the saponification process, especially when working with reactive ingredients or complex formulations.
Temperature Synchronization Methods
Achieving proper temperature balance between oils and lye stands as one of the most critical factors in successful soap making. When your components aren't properly synchronized, you'll risk improper saponification and potentially flawed batches.
You'll need to guarantee both elements reach similar temperature ranges, typically between 100°F and 120°F.
To effectively synchronize temperatures:
- Use a double boiler method to control heat application to your oils, preventing overheating while maintaining consistent temperature.
- Apply a warm water bath to gradually adjust the temperature of your cooler component, usually the lye solution.
- Preheat oils in the oven at a low temperature setting to help match your lye solution's temperature, especially useful in cooler environments.
Always monitor both components with a reliable thermometer, aiming for less than five degrees variance between them.
Preventing Soap Seizing
Temperature synchronization serves as the foundation for another important aspect of soapmaking: preventing soap seizing. You'll gain better control over your soap mixture by keeping oils and lye at similar temperatures (100-110°F). This balance prevents sudden temperature drops that can trigger rapid saponification.
For ideal results, use your stick blender in short bursts to avoid generating excess heat. Small batch processing makes temperature management easier and reduces seizing risks.
Prevention Strategy | Benefits |
---|---|
Heat treating oils | Stabilizes temperatures across ingredients |
Adding sodium lactate | Slows saponification rate |
Short blender bursts | Prevents overheating during mixing |
Oil combination balancing | Creates more forgiving temperature window |
Remember that monitoring your mixture's temperature throughout the process is essential—excessive heat differences between components remains the primary cause of seized soap.
Insulation Techniques for Cold Process Methods
While managing heat loss presents considerable challenges in cold process methods, proper insulation techniques can dramatically improve thermal efficiency and process control.
Effective insulation minimizes heat transfer and maintains consistent temperatures throughout your batch processing, resulting in more predictable outcomes.
- Wrap your vessels with insulating materials – Fiberglass, mineral wool, or ceramic fiber provide excellent thermal resistance, considerably reducing heat loss during critical processing phases.
- Implement double-wall construction – Create an air gap between interior and exterior walls to enhance insulation and minimize unwanted temperature fluctuations.
- Apply heat-reflective barriers – Strategic placement of foil wraps or high-temperature resistant blankets around key components reflects radiant heat back into your process, improving overall thermal efficiency and reducing energy requirements.
Using Water Discounts to Control Reaction Heat
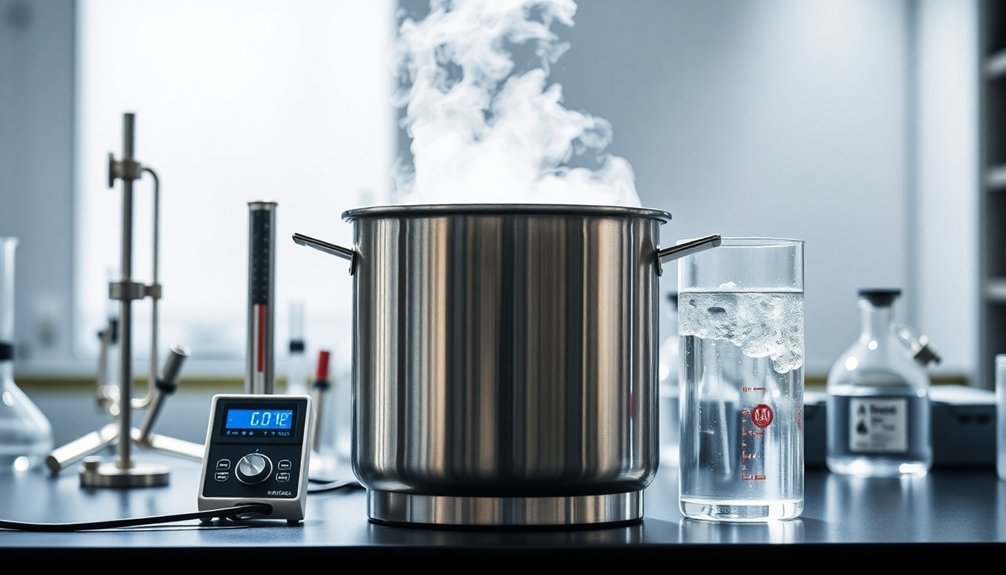
Beyond physical insulation methods, chemical adjustments offer powerful ways to manage batch heat. Water discounts—reducing the amount of water in your reaction mixture by 5-15%—can effectively control exothermic heat while enhancing your process efficiency.
When you implement water discounts, you're creating a more concentrated reactive environment that actually improves reaction kinetics while maintaining safer temperature conditions. Your reaction heat becomes more predictable and manageable as the reduced water volume requires less energy to heat.
Monitor your mixture's specific heat capacity closely, as water content directly affects heat transfer characteristics.
For best results, adjust your water discount percentages based on real-time temperature readings throughout the process. This dynamic approach helps you maintain ideal reaction conditions by balancing heat generation with removal capacity, preventing unwanted side reactions or product degradation.
Optimal Mixing Speeds to Prevent Temperature Spikes
Proper agitation plays a critical role in heat distribution throughout your batch process, directly affecting temperature uniformity and reaction control.
Finding ideal mixing speeds guarantees effective heat transfer while preventing dangerous temperature spikes that could compromise product quality.
- Maintain speeds between 100-300 RPM for most liquid batches to achieve balanced heat distribution without excessive shear that generates unwanted heat.
- Invest in a variable speed mixer that allows you to adjust agitation based on your mixture's viscosity, helping maintain consistent temperatures as batch properties change.
- Monitor temperature at multiple points throughout your vessel and be prepared to adjust mixing speeds accordingly, especially when using external heating sources like thermal jackets.
Choosing Fragrance Oils That Won't Accelerate Trace

Why do some batches seize up minutes after adding fragrance while others remain workable for complex designs? The secret lies in selecting the right fragrance oils for your soap recipes.
Look for oils specifically labeled as "non-accelerating" or "slow-moving" to maintain a manageable trace during saponification. Lighter scents like citrus typically behave better than rich ones like vanilla.
Fragrance Type | Behavior | Best For |
---|---|---|
Citrus/Herbal | Slow-moving | Intricate designs |
Floral/Mint | Moderate | Most recipes |
Spice/Vanilla | Fast-moving | Simple pours |
Always test small batches first, as your specific recipe may react differently. Review supplier descriptions carefully—many provide detailed information about acceleration tendencies. Working at cooler temperatures further helps control how your fragrance oils affect trace time.
Frequently Asked Questions
How Do Additives Like Colorants Affect Batch Heat Regulation?
Colorants can increase your batch heat by absorbing more energy. You'll need to adjust cooling systems or mixing speeds to compensate. Some darker additives retain more heat, requiring extra vigilance during processing.
Can External Cooling Methods Be Used During Trace Acceleration?
Yes, you can use external cooling methods during trace acceleration. Placing your container in an ice bath, using a fan, or working in a cool environment will help manage heat spikes when your soap begins thickening.
What Temperature Monitoring Tools Are Most Accurate for Soapmaking?
Digital infrared thermometers and thermocouple probes are most accurate for soapmaking. You'll get the best results using probes for liquid temps and infrared guns for quick surface readings. Don't rely on candy thermometers.
How Does Altitude Impact Soap Batch Heating Requirements?
At higher altitudes, your soap batches will heat differently due to lower boiling points. You'll need to reduce your heating temperatures by about 1°F per 500 feet above sea level to avoid overheating issues.
When Should Emergency Heat Reduction Techniques Be Implemented?
Implement emergency heat reduction when you're seeing rapid temperature increases, volcano-like swelling, or your batch exceeds 200°F. Don't wait – act immediately when you notice these warning signs to prevent ruined soap or safety hazards.
In Summary
By mastering these seven techniques, you'll gain complete control over your soap's batch heat. Whether you're adjusting pot sizes, managing temperatures, or selecting the right fragrance oils, you're now equipped to prevent overheating issues. Remember, controlling heat isn't just about avoiding problems—it's about creating consistent, high-quality soap every time. Trust your new skills and don't be afraid to experiment with these methods in your next batch.
Leave a Reply