Start with a 10% water discount to improve your cold process soap's quality and appearance. You'll experience faster unmolding, harder bars, and fewer aesthetic issues like glycerin rivers and soda ash. Keep your lye solution strength between 25-33% for ideal results, and adjust temperatures below 95°F to manage trace. Mix fragrances into oils first to prevent acceleration, and maintain proper ventilation during curing. These fundamental tips will set you up for soap making success, but there's much more to master.
Start With a 10% Water Discount
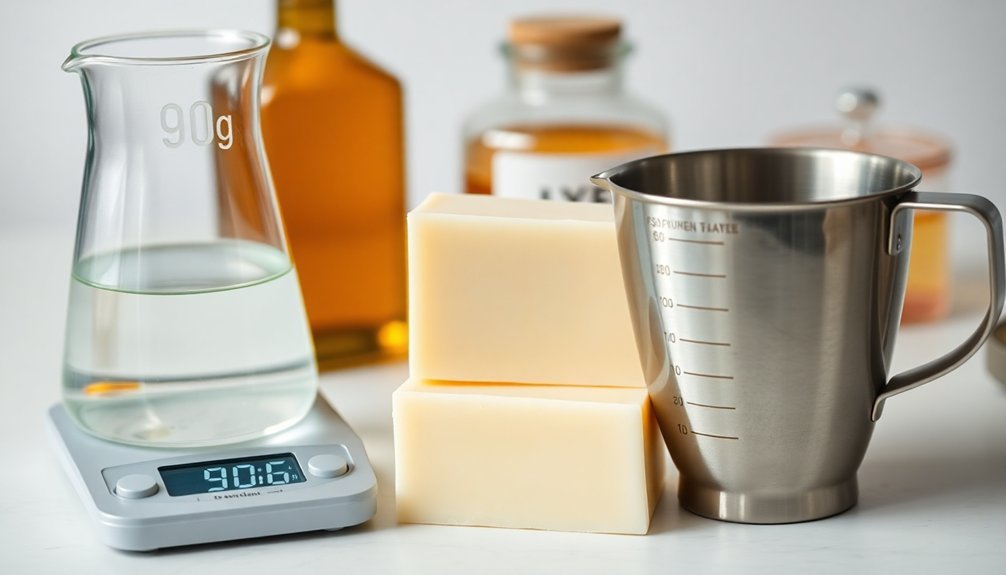
Three key benefits make a 10% water discount an ideal starting point for cold process soap making.
You'll notice faster mold release times, as your soap will be easier to unmold and handle without sticking. The reduced water content speeds up the curing process considerably, resulting in harder, longer-lasting bars that are ready to use sooner than the typical 4-6 week period. Using a higher lye concentration helps the soap achieve trace more efficiently.
You'll also achieve better aesthetic results with fewer issues like soda ash and glycerin rivers, leading to more visually appealing soap.
Keep in mind that this water reduction will cause your soap batter to trace more quickly, which affects your design options. While this faster trace might limit intricate patterns initially, it can actually help create more distinct layers in your simpler designs.
Calculate Your Lye Solution Strength
To calculate an effective lye solution strength, you'll need to know your base ratios, such as using a 2:1 water-to-lye ratio for a 33% solution or 3:1 for a 25% solution.
You must measure your lye with absolute precision using an accurate scale, as even small variations can greatly affect your final soap. Understanding whether to use NaOH or KOH will determine your final product type.
Your water-lye concentration directly impacts your soap's trace time and curing period, so consider starting with a 28% solution for a balanced approach that provides good workability while maintaining reasonable cure times.
Know Your Base Ratios
Understanding lye solution strength is fundamental for achieving your desired soap qualities and curing times. The two most common base ratios you'll encounter are 25% and 33% solutions.
A 25% solution (75% water) gives you maximum workability but longer curing times, while a 33% solution (67% water) speeds up curing and produces harder bars sooner. Using less water amounts can significantly decrease trace time.
You can easily calculate your water amounts using multipliers. For a 33% solution, multiply your lye weight by 2; for a 25% solution, multiply by 3.
For example, if you're using 3.5 oz of lye in a 33% solution, you'll need 7 oz of water. Remember, you can't go below a 1:1 water-to-lye ratio, as lye needs at least an equal amount of water to dissolve properly.
Measure Lye With Precision
Precise measurement and calculation of your lye solution strength directly impacts your soap's final quality.
You'll need to understand how to measure your lye-to-water ratio to achieve consistent results. For example, if you're using a 33% solution, multiply your lye weight by 2 to determine your water amount. Higher superfat percentages will require a less concentrated lye mixture for optimal results.
Consider these key ratios for your soap making process:
- A 25% solution (multiply lye by 3) gives you plenty of working time but requires longer curing.
- A 33% solution (multiply lye by 2) offers a balanced approach for most recipes.
- A 40% solution (multiply lye by 1.5) speeds up trace and reduces cure time.
Don't go beyond a 50% solution, as your lye won't properly dissolve.
Assess Water-Lye Concentration
Calculating your lye solution strength involves a simple but essential formula that guarantees your soap's success. To determine your water amount, multiply your lye weight by the appropriate ratio for your desired concentration. For example, if you're aiming for a 33% solution, multiply your lye weight by 2; for 25%, multiply by 3.
You'll want to take into account your goals when choosing your concentration. Higher concentrations (40-50%) will speed up trace and cure times, creating harder soaps faster. However, don't exceed 50%, as the lye won't fully dissolve. Understanding caustic soda ratios is critical for achieving proper saponification in your soap making process.
Lower concentrations (25-28%) slow the process but guarantee complete saponification. Remember to keep your solution above 25°C (77°F) to prevent lye from precipitating out, especially with stronger concentrations.
Adjust for Fragrance Acceleration
When working with fragrance oils that accelerate trace, adjusting your water discount requires careful consideration.
You'll need to balance the benefits of water discounting against the challenges of working with fast-moving fragrances. A higher water content can help counteract acceleration, while reducing your water discount will speed up trace even more.
For best results with accelerating fragrances:
- Mix your fragrance into your oils before adding lye
- Keep temperatures below 95°F
- Use more slow-moving oils like olive, sunflower, or rice bran
You can also adapt your workflow by preparing all colorants in advance, using a whisk instead of a stick blender, and having your molds ready before you begin.
If you're new to soaping, consider using full water amounts until you're comfortable managing acceleration.
Master Quick Trace Management
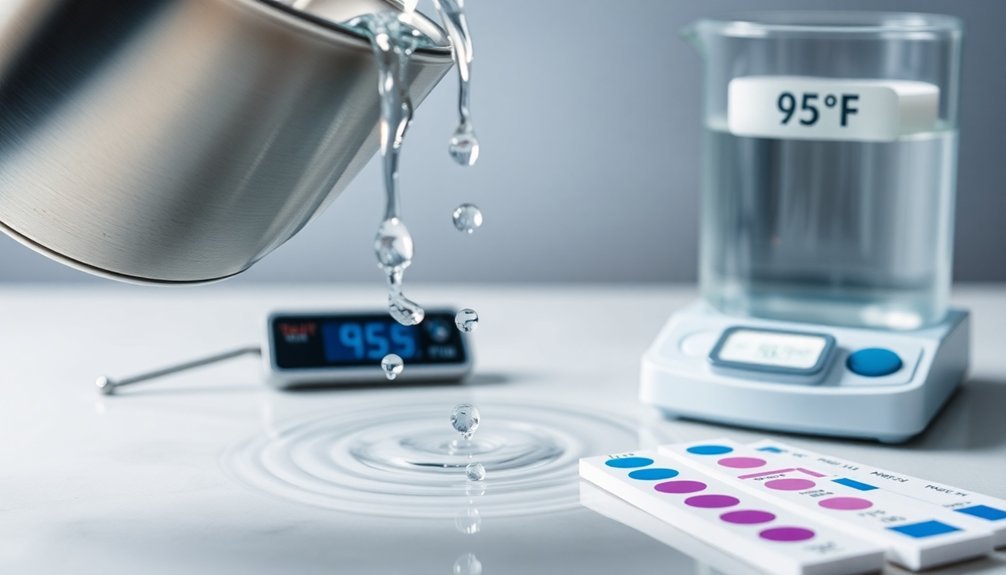
Beyond managing accelerating fragrances, mastering quick trace requires understanding multiple variables that affect your soap's setting speed.
You'll get better control by adjusting your oil choices and temperatures strategically. Opt for liquid oils like olive and almond to slow trace, while limiting hard butters and coconut oil that speed up the process.
Keep your soaping temperatures between 80-90°F for ideal control, and use an infrared thermometer for accurate readings.
When working with water discounts, remember that less water means faster trace – start with a modest 10-15% discount.
Your mixing technique matters too; use your stick blender in short bursts rather than continuous blending. If you need more working time, hand stirring can greatly slow the process, giving you extra time for intricate designs.
Prevent Glycerin Rivers and Soda Ash
Two common challenges in cold process soapmaking – glycerin rivers and soda ash – can be effectively managed through proper water discounting.
You'll prevent glycerin rivers by using a 10-15% water discount, which reduces the amount of water that needs to evaporate during curing. For soda ash prevention, consider increasing your water discount up to 30%.
Your success in preventing both issues depends on careful temperature control and additive management.
Watch for these telltale signs:
- Whitish, vein-like patterns appearing in your soap (glycerin rivers)
- A powdery white film on your soap's surface (soda ash)
- Overheating or uneven cooling in your molds
Remember to adjust your water discount when using water-rich additives like milk or fruit juices, and choose fragrances that won't cause overheating in your batch.
Balance Additives and Water Content
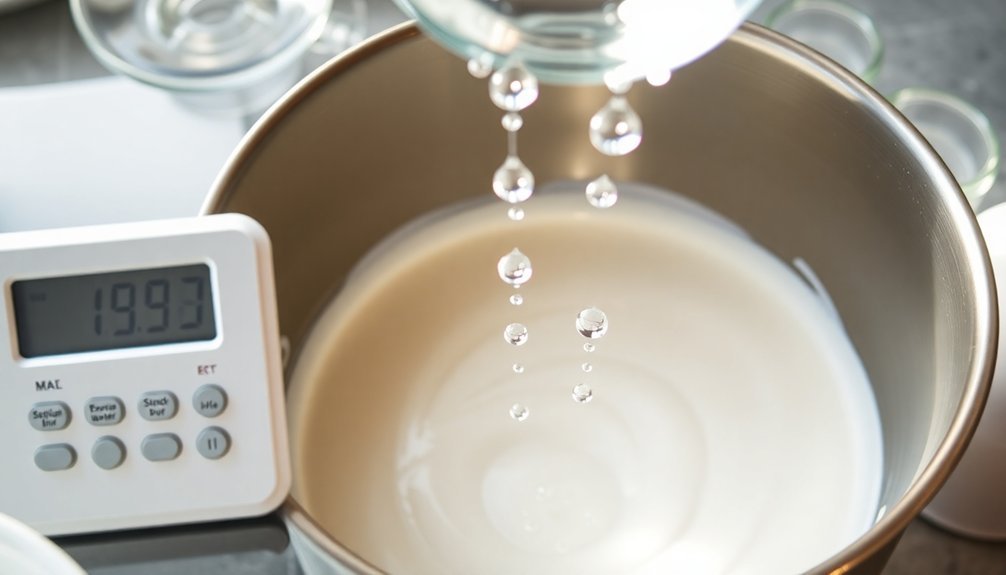
To properly balance your soap's moisture content, you'll need to measure all liquid additives like purees or juices first.
Calculate the total moisture from these add-ins plus your water, keeping in mind that most fruit and vegetable purees contain 80-95% water.
You can then adjust your lye solution accordingly, maintaining a minimum 2:1 water-to-lye ratio while accounting for the moisture from your additives.
Measure Liquid Add-Ins First
Measuring liquid add-ins accurately stands as your first critical step in successful CP soap making.
You'll need to account for the water content in additives like fruit purees and vegetable juices before calculating your final water discount. This helps you maintain the right water-to-lye ratio and prevents your soap from becoming too soft or developing glycerin rivers.
Consider these key factors when measuring your liquid add-ins:
- Each fruit or vegetable puree contributes hidden water that affects your total moisture content
- Your lye solution's concentration should stay between 1.5 to 3 times the amount of water to lye
- Extra moisture from additives can increase curing time and impact your soap's final texture
Calculate Total Recipe Moisture
Since every liquid component affects your final soap's properties, calculating the total recipe moisture requires careful consideration of both your water-to-lye ratio and any additional liquid ingredients.
You'll need to start with at least a 1:1 water-to-lye ratio, though many soapmakers prefer higher ratios like 2:1 for better control.
Consider your oil choices when determining water content. Different oils have varying saponification values and moisture needs – coconut oil demands more water than olive oil.
If you're superfatting your recipe, you'll want to account for how these extra oils impact the overall moisture balance.
Remember that your final water percentage (typically around 38% of oils) should support proper saponification while achieving your desired bar hardness.
You can adjust this based on your specific recipe requirements and curing plans.
Adjust Lye Solution Accordingly
The proper adjustment of your lye solution creates the foundation for successful water discounting in cold process soap.
When working with water-rich additives like fruit purees or vegetable juices, you'll need to account for their moisture content in your overall recipe. Start with a 10-15% water discount to prevent your soap from becoming too soft or taking too long to cure.
- A 33% lye solution offers an ideal balance for most recipes, providing manageable trace times and controlled gel phases.
- A 40% solution speeds up trace and curing but requires quick work and careful handling.
- A 25% solution gives you more working time but extends the curing period.
Remember to maintain a safe water-to-lye ratio between 1:1 and 3:1, and always use a lye calculator to verify your measurements are precise.
Monitor Temperature Control
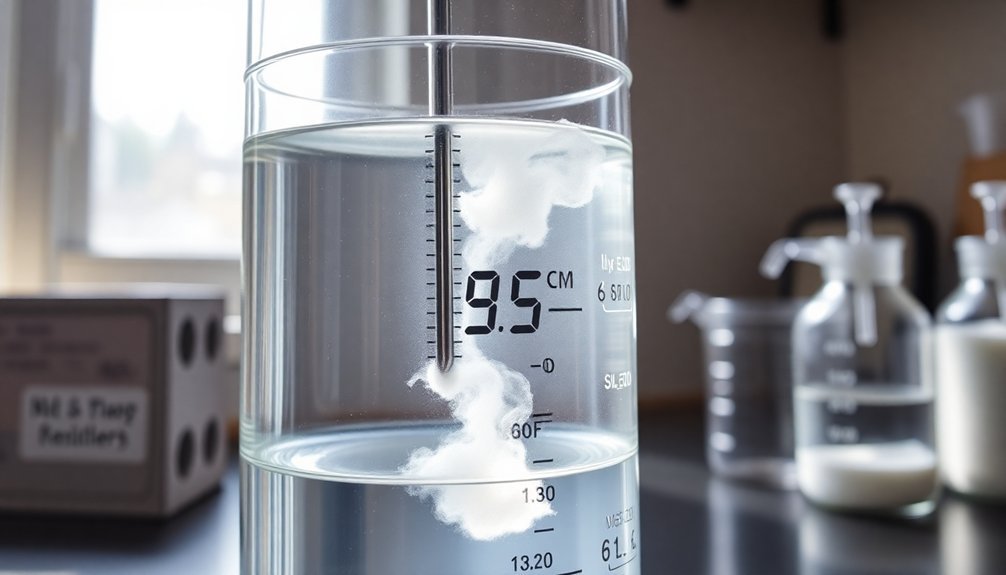
Maintaining precise temperature control plays an essential role when making cold process soap with water discounts. You'll want to keep temperatures below 110°F to prevent accelerated trace and potential separation issues.
When using the heat transfer method, let the temperature naturally drop as you add your hard oils and butters, typically settling between 99-113°F.
Monitor your temperatures carefully with an infrared thermometer throughout the process. If you're working with hard oils or stearic acid, lower temperatures will give you more control and working time.
Don't worry about matching your lye solution and oil temperatures exactly – this isn't necessary for successful soap making.
For controlled gel phase, you can preheat your oven to 110°F, turn it off, and place your mold inside, or use insulation methods if desired.
Create Harder, Longer-Lasting Bars
Your water discount choices directly impact how fast your soap bars harden and how long they'll last.
You'll get firmer bars more quickly by reducing water to 25-35% of your total recipe, allowing you to use your soap sooner than traditionally cured bars.
Beyond faster unmolding and curing, proper water reduction creates milder, longer-lasting bars that won't dissolve as quickly during use.
Maximize Water Reduction Benefits
By reducing water content in your CP soap recipe, you'll create considerably harder bars that last longer and cure faster.
The lower initial moisture content helps prevent your bars from becoming soft or mushy over time, while enhancing their overall durability and resistance to wear and tear.
You'll notice these visual and performance benefits when using water reduction:
- Fewer glycerin rivers, especially in recipes containing titanium dioxide
- Minimal soda ash formation on the soap's surface
- More uniform appearance, particularly in soaps with fruit or vegetable purees
The technique requires careful attention since it creates a faster-moving trace.
While the soap's feel remains unchanged, you'll appreciate how quickly you can unmold your bars.
Quick Cure Time Advantages
One of the most compelling benefits of water discounting is the considerably reduced cure time for your CP soap bars. You'll create harder bars that cure up to 2 weeks faster while gaining improved lather and longevity. By using less water, your bars will resist disintegration and maintain their shape better during use.
Feature | Benefit |
---|---|
Faster Drying | Bars lose weight quickly, indicating accelerated cure |
Better Texture | Enhanced lather quality and bar hardness |
Extended Life | Improved resistance to softening and dissolution |
Skin Benefits | Maintains mildness and moisturizing properties |
To speed up the process even further, you can use dehumidifiers or fans to improve airflow around your bars. Monitor your soap's progress by weighing them regularly and storing them in a dry, well-ventilated area.
Perfect Your Layering Technique
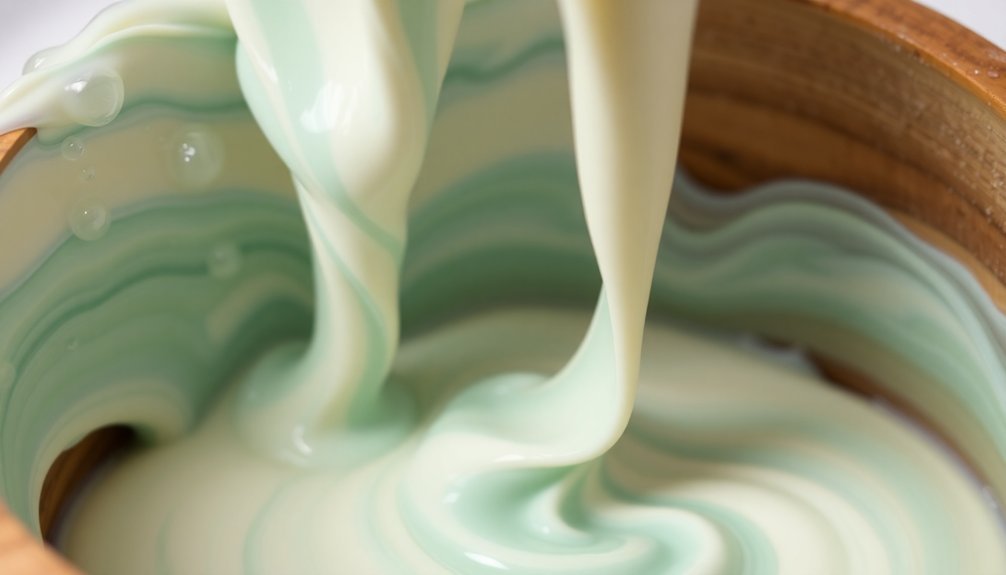
The perfect layering technique combines artistry with precision, requiring careful attention to trace consistency and temperature control.
Keep your soap batter at a light to medium trace and maintain temperatures between 85-90°F for best results. You'll need separate mixing pitchers and silicone spatulas for each layer to prevent color contamination.
Create stunning gradient effects by:
- Starting with your darkest base color and gradually lightening it for subsequent layers
- Using a spatula to flood-fill each layer, preventing breakage
- Working quickly but carefully to maintain consistent layer thickness
Use your immersion blender sparingly – just enough to achieve the right trace.
For added visual interest, you can incorporate soap shreds or mica solutions between layers. Remember, you can reverse the gradient by starting with your lightest color first.
Optimize Cure Time Reduction
Reducing cure time for cold process soap requires a strategic combination of water discounting and environmental control.
Start by cutting your water content by 7-10% to shorten the cure time to about three weeks while creating harder, longer-lasting bars.
Create ideal curing conditions by placing your soaps in a well-ventilated area with good airflow.
You'll achieve faster results by using a dehumidifier to remove excess moisture from the air.
Add a small heater fan to speed up the evaporation process, especially during cooler months.
Track your progress by weighing soap bars regularly to monitor water loss.
Don't wrap or box your soaps until they're fully cured.
Frequently Asked Questions
Can I Use a Water Discount With Milk-Based Soap Recipes?
You can use water discounts in milk-based soaps, but it's risky. Keep discounts minimal (10-15%) since milk adds heat to your mixture. It's safer to maintain full water amounts to prevent scorching.
How Does Humidity Affect the Water Discount Calculation?
You'll need to adjust your water discount based on humidity levels. In high humidity, use smaller discounts since evaporation is slower. In low humidity, you can use larger discounts as water evaporates faster.
Should Water Discounting Be Adjusted for Different Oil Combinations?
Yes, you'll need to adjust water discounting based on your oil combinations. Hard oils like palm and coconut require less discount, while liquid oils like olive can handle more aggressive discounting for ideal results.
Does Water Discounting Affect the Final Ph of Soap?
No, your soap's final pH won't be affected by water discounting. The pH level is determined by the lye-oil saponification process, not water content. You'll still achieve the same pH regardless of water amounts.
Can Water Discounting Help Prevent Soap Sweating in Humid Climates?
Yes, you'll find water discounting helps reduce soap sweating in humid climates. By using less water in your recipe, you're creating a drier soap that's less likely to attract moisture from humid air.
In Summary
By mastering water discounting in your CP soap making, you'll create harder bars that cure faster and perform better. You've learned techniques from basic 10% discounts to advanced temperature control and layering methods. Remember to always calculate your lye solution carefully and adjust for fragrances. With these skills, you're ready to craft superior soaps with fewer imperfections and improved longevity.
Leave a Reply