For cold process soap, you'll want to use fragrance oils at 5-6% of your base oil weight (about 0.7 ounces per pound of oils). Calculate this using only your oil weight, not including lye or water. For example, with 16 ounces of base oils, you'd use 0.8 ounces of fragrance oil at a 5% load. Always check your supplier's guidelines and IFRA recommendations, as some fragrances require lower usage rates. Master these basic calculations, and you'll reveal the secrets to perfectly scented soaps.
Understanding Fragrance Oil Calculations
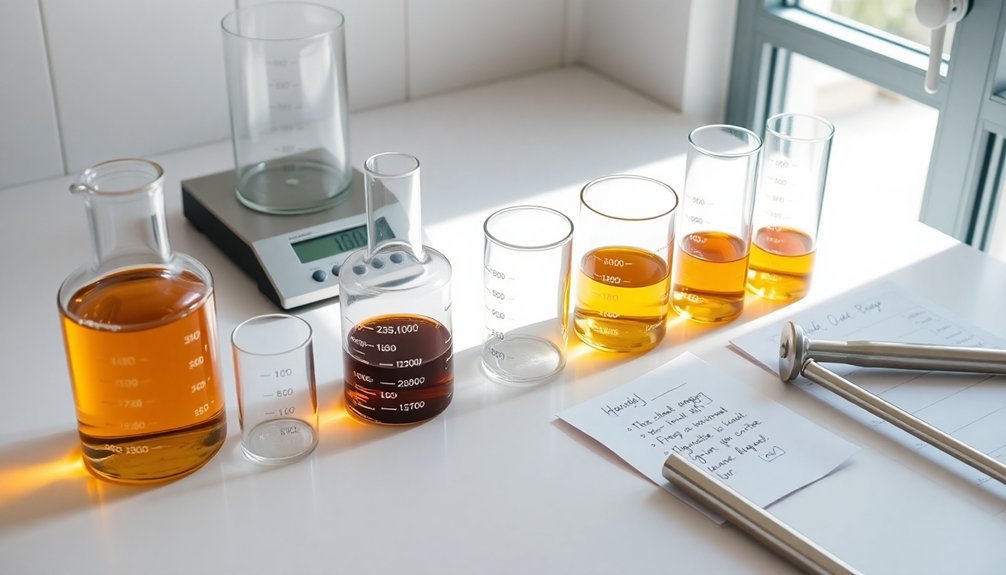
Three key factors determine how to calculate fragrance oil amounts for cold process soap: the base oil weight, recommended usage rates, and proper unit conversions.
You'll need to calculate your fragrance oil amount based on the weight of your base oils only, not including the lye or water weight in your recipe.
For example, if you're using 16 ounces of base oils and want a 5% fragrance load, you'll need 0.8 ounces of fragrance oil.
When working in grams, simply calculate the same percentage of your total oil weight – 5% of 500g would be 25g of fragrance.
For cold process soap making, 0.7 ounces per pound is the standard recommended fragrance amount for optimal scenting.
Most suppliers recommend fragrance loads between 5% and 12%, but you should always check their specific guidelines and IFRA recommendations for the safest, most effective results.
Essential Safety Guidelines for Fragrance Loads
When working with fragrance oils in your cold process soap, you'll need to follow IFRA Category 9 guidelines, which set specific safety limits for bath and body products.
Your fragrance load calculations must be based on the final cured weight of your soap to guarantee you're not exceeding these safety thresholds.
Most experienced soap makers find that 5% to 6% fragrance provides optimal results in their finished soaps. If your chosen fragrance has an IFRA limit below 6%, you may need to select a different scent or adjust your formula, as these restrictions could prevent you from achieving a strong enough scent while maintaining safety standards.
IFRA Category 9 Standards
Understanding IFRA Category 9 standards is essential for safe soap making, as these guidelines specifically govern products like bar soaps, bath gels, and other rinse-off items that contact sensitive skin areas.
When you're calculating fragrance loads, you'll need to base your measurements on the total weight of your finished product, not just the oils.
While IFRA certificates provide maximum usage rates, you should consider both safety limits and your soap's performance needs. A typical fragrance load percentage of 3-6% is recommended for most cold process soaps. You'll find that some fragrances might need less than the maximum allowed amount to work well in your recipe.
Remember to test your fragrances in small batches first, as they can behave differently in cold process soap.
Always prioritize IFRA safety guidelines over scent strength, even if your base formula could technically hold more fragrance.
Maximum Safe Usage Rates
Safe fragrance loads in cold process soap require strict adherence to established guidelines, with most formulations capping usage at 3% of your oil weight. This limit helps prevent skin irritation, soap instability, and other potential issues that can arise from overloading your product.
While you'll find varying recommendations from suppliers, always prioritize IFRA guidelines as your safety benchmark. Regular exposure to high fragrance concentrations can lead to developing severe allergic reactions. Calculate your fragrance load based on the weight of your oils and butters, not the total soap weight.
You'll need to test each fragrance oil carefully, as some can cause seizing or ricing at higher concentrations. Keep detailed records of your tests and remember that using more fragrance isn't always better.
You'll achieve the best results by finding the sweet spot between scent strength and soap stability while maintaining safety standards.
Calculating the Perfect Fragrance Amount
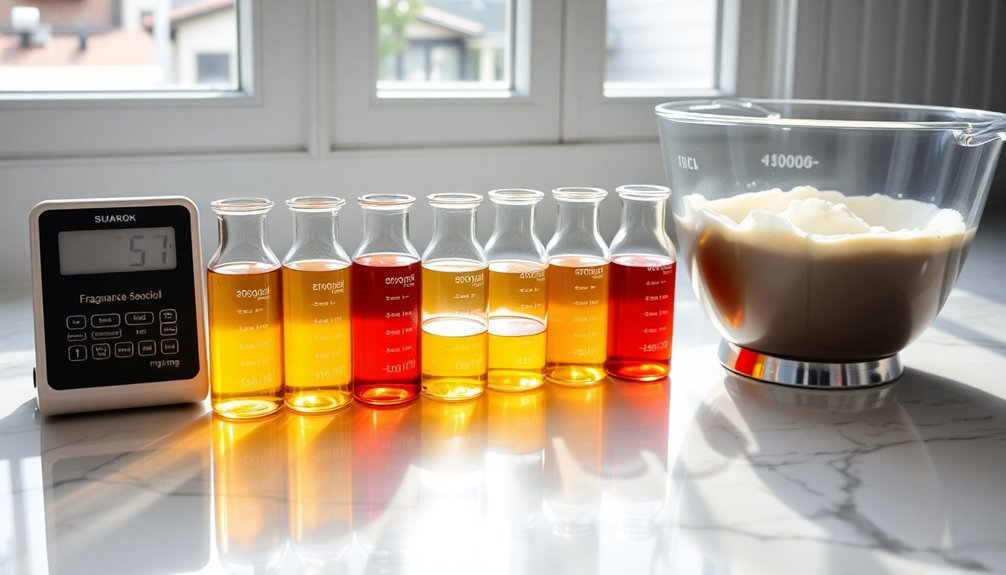
Achieving the perfect fragrance balance in cold process soap requires precise calculations based on your total batch weight.
You'll need to add up all ingredients, including oils, lye, and water, to determine your base weight before calculating fragrance amounts.
To find your fragrance oil quantity, multiply your total batch weight by your desired fragrance percentage. Most soapmakers use between 2% to 5%, depending on the specific fragrance oil and IFRA guidelines.
For example, if you're making a 20-ounce batch and want a 2.5% fragrance load, you'll need 0.5 ounces of fragrance oil.
Don't forget to take into account your fragrance oil's specific properties. Some oils contain vanillin that can discolor, while others may accelerate trace. For optimal temperature control and consistent results, blend your oils and lye water at 110ºF or lower.
It's wise to test new fragrances in small batches first.
Common Mistakes in Fragrance Measurements
You're likely to face two critical pitfalls when measuring fragrance oils for cold process soap: adding too much fragrance and using incorrect calculation methods.
Using excessive fragrance oil can lead to skin irritation and unstable soap, while eyeballing measurements instead of using precise calculations will produce inconsistent results.
To avoid these issues, you'll need to use a digital scale and follow recommended usage rates, typically between 3-6% of your total oil weight.
Too Much Fragrance Added
The sweet aroma of homemade soap can quickly turn sour when too much fragrance oil is added to a batch.
You'll face several issues when overdoing fragrance oils, including seizing, ricing, and separation of your soap batter. Most significantly, your soap may become crumbly or develop an uneven texture due to disrupted saponification.
Beyond texture problems, excessive fragrance can cause skin irritation and create an overpowering scent that's uncomfortable to use.
To avoid these pitfalls, always follow IFRA guidelines and recommended usage rates based on your total oil amount. It's essential to test new fragrances in small batches first and keep detailed records of successful ratios.
Remember that different fragrances have varying safe usage rates, so don't assume one size fits all when measuring your scents.
Wrong Calculation Methods
When soapmakers calculate fragrance amounts incorrectly, their entire batch can suffer from inconsistent scenting or safety issues. A common mistake is basing fragrance calculations on total recipe volume instead of base oil weight, which doesn't account for water evaporation during curing.
You'll need to measure your fragrances by weight, not volume, using a reliable digital scale. Avoid syringes or pipettes that can retain scents and compromise accuracy.
Don't forget to check IFRA guidelines and safety rates for each essential oil – especially potent ones like clove and cinnamon bark that require lower usage rates.
Consider how your other ingredients affect scenting. Coconut oil, palm oil, and additives like clay can impact fragrance distribution.
Deodorized butters may alter your scent's final outcome, so factor these interactions into your calculations.
Testing Your Fragrance Oil Ratios
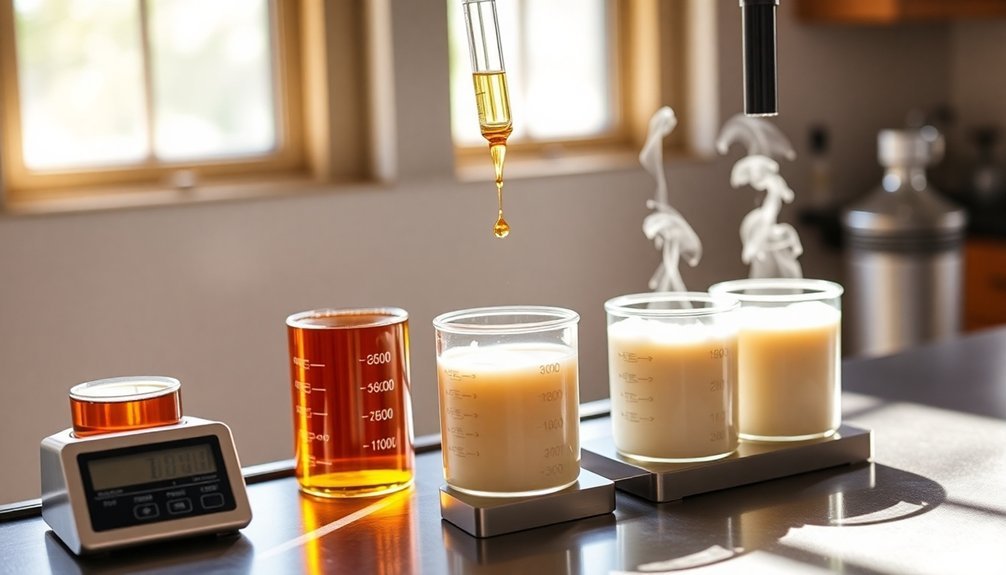
Successfully testing fragrance oil ratios requires a systematic approach and careful documentation of results. You'll need to prepare multiple small batches using a standardized recipe and test each fragrance against a control sample. Start with 5% fragrance oil unless IFRA guidelines specify otherwise.
Test Factor | What to Watch | When to Check |
---|---|---|
Acceleration | Batter setup speed | During mixing |
Ricing | Rice-like particles | While pouring |
Discoloration | Color changes | Throughout cure |
Keep your oils and lye water at 110°F or lower, and use a 2:1 water-to-lye ratio. Document scent strength, changes in odor, and any discoloration during the process. After unmolding in 24-72 hours, let your soap cure for four weeks before making your final evaluation. Your testing records should reflect specific dates, recipes, and any variations in results.
Adjusting Ratios for Different Oil Bases
Making fragrance oil adjustments requires careful consideration of your soap's oil base composition, as different oil combinations can greatly affect how fragrances perform.
When you're working with recipes high in olive oil, you'll need to account for its slower trace and potential impact on fragrance stability. Similarly, coconut oil's quick-tracing nature can affect how your fragrance behaves during saponification.
You'll want to maintain a balanced ratio of saturated to unsaturated fats (around 40:60 or 45:55) while adjusting your fragrance amounts.
If you're substituting oils, remember that few are directly interchangeable – except for oils with similar fatty acid profiles, like palm and tallow.
Use a soap calculator to guarantee your adjustments maintain consistent quality, and always document your changes to track how different oil combinations affect your fragrance performance.
Documenting Your Fragrance Results
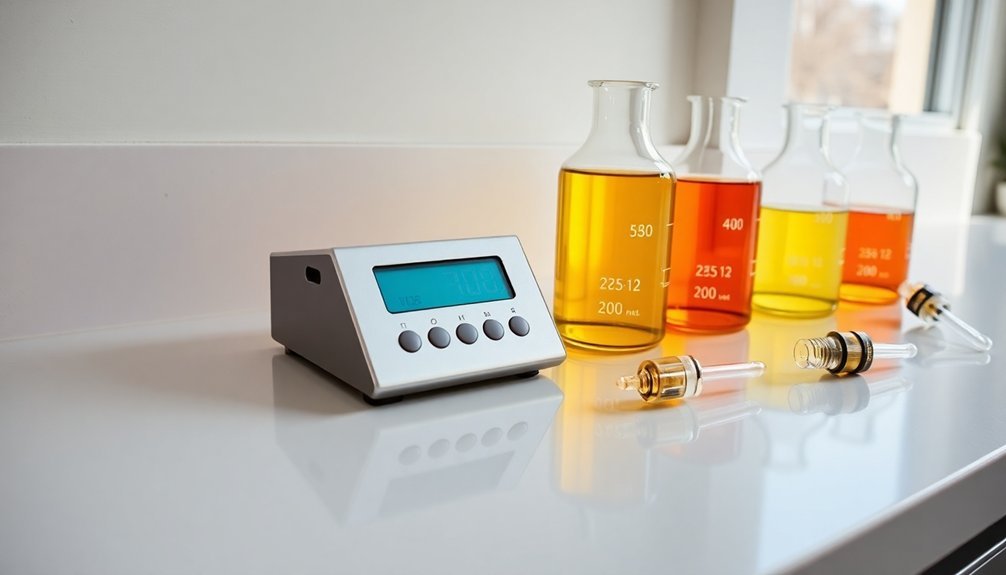
Proper documentation of your fragrance testing serves as a valuable roadmap for future soap batches.
You'll want to record your observations at key stages using the standardized recipe with 40% Olive Oil Pomace, 25% Coconut Oil, and the remaining specialty butter blend.
Critical documentation points include:
- Initial mixing behavior – note any acceleration, ricing, or separation when you add the fragrance at 5% (or IFRA-specified levels)
- Post-unmolding assessment – document scent strength, color changes, and odor profile between 24-72 hours
- Four-week cure results – evaluate final scent retention and any discoloration
Remember to test at consistent temperatures (110°F or lower) and use a 2:1 water-to-lye ratio.
Label each test batch with the date to track which recipe version you've used, ensuring your documentation stays organized and reliable.
Troubleshooting Fragrance Issues
When working with fragrance oils in cold process soap, you'll likely encounter several common issues that require troubleshooting.
If your soap batter seizes or accelerates, switch to a hand whisk instead of an immersion blender and consider adding the fragrance to your melted oils before combining with lye.
Watch for ricing, which creates rice-like lumps when fragrance oils bind with hard fats. You can blend these out, but be prepared for the batter to thicken.
If separation occurs, try re-blending the mixture. For persistent issues, you may need to rebatch.
To minimize problems, always purchase fragrance oils from reputable suppliers, check other soapmakers' reviews, and test new fragrances in small batches.
Remember that floral and spice scents often cause acceleration, while certain fragrances can lead to discoloration.
Frequently Asked Questions
Can I Blend Multiple Fragrance Oils to Create Custom Scents?
Yes, you can blend multiple fragrance oils to create unique custom scents. Start with small test batches, experiment with different ratios, and verify your oils are compatible before mixing them together.
Why Do Some Fragrances Fade Completely During the Curing Process?
Your fragrances can fade completely during curing because of high pH levels attacking the oil components, exposure to heat above flash points, and chemical reactions. You'll notice this especially with volatile essential oils.
How Do Seasonal Temperature Changes Affect Fragrance Oil Performance?
You'll notice your fragrance oils perform differently across seasons. High summer temperatures can accelerate scent fading and alter oil stability, while cold winters may slow down scent release and affect overall fragrance performance.
Should Fragrance Calculations Change When Using Milk-Based Soap Recipes?
No, you don't need to change your fragrance calculations for milk soaps. Keep calculating based on the total oil weight, not total recipe volume. Milk's water content doesn't affect your fragrance oil measurements.
Can I Add Fragrance Oils to Rebatched Soap Successfully?
Yes, you can add fragrance oils to rebatched soap. You'll need to mix them thoroughly into the melted soap at 0.7-1 oz per pound of oil, but be aware that heat may affect scent strength.
In Summary
Finding your perfect fragrance oil ratios takes patience and careful documentation. You'll need to reflect on your base oils, safety guidelines, and personal scent preferences. Don't be afraid to experiment within safe limits, but always record your results. Start with conservative amounts and adjust gradually. Once you've mastered the basics of fragrance calculations, you'll create consistently scented soaps that your customers will love.
Leave a Reply